- It includes many free speaker plans -- mostly single driver/full range, random info (hopefully useful), links to sites with other useful info. I will endeavor to keep adding more info as it comes along.
- Sound Tsao FA8 Alnico magnet full-range speakers ( Walnut ) TQWT floor boxes. Sound Tsao FA8 Alnico magnet full-range speakers ( Walnut ) TQWT floor boxes. Wooden Speakers, Built In Speakers, Bookshelf Speakers, Stereo Speakers, Desktop Speakers, Diy Speakers, Speaker Design, Audio Design. Visaton BG 20 Single Driver Full Range Speakers.
- Driver Single Hex Nut One Quarter
- Full Range Driver Single Tqwt Diy Slime Recipe
- Icd 10 Mva Driver Single Vehicle
- Full Range Driver Single Tqwt Diy Slime Kit
- Trolley Driver Single Coin Dispenser
- Car And Driver Single Car Seat Cover
22_september_15 Introduction Frugal-Horn.com is a home of high-performance, low-cost (ie frugal) diy horn designs. The resurgence of interest in full range speakers has led to a renewed exploration of the rear-loaded horn. Jan 10, 2019- Sound Tsao FA8 Alnico magnet full-range speakers ( Walnut ) TQWT floor boxes.
This is the Voight-Pipe Resource Page. I created it because I didn't want information about this speaker design to be lost. The original web site that caught my interest in this do-it-yourself speaker design has long since disappeared, though its influence is considerable (if the number of references to it by other people are any guide). Sadly that site and the many images of other Voight-Pipe builders is no longer available on the web. So, one day I took the time to follow every link and lead I could find via Google and I copied text and images to my local web site. I built this page as I went along. Here you'll find an explanation about the Voight-Pipe's design (also called a TQWT or Tapered Quarter Wavelength Tube design). You'll also find several careful explanations, some with copius photographs, of Voight-Pipe builds. There are schematics for the speaker housing construction. There is discussion about the type of driver to use (some use Fostex, some use Radio Shack, and others use Lowther). There are graphs of the finished speaker's sonic characteristics. There are testimonials about the sound the speakers produce. If any reader who finds this page knows of other Voight-Pipe information on the web, please email me at stal_g@yahoo.com and I'll include it here.
What's here:
TQWT/QWT

First described by Paul Voigt in 1930, TQWT/QWT uses like a transmission line design pipe lenght of 1/4 wavelenght of driver's resonance frequency. TQWT and QWT stands for (tappered) quarter wave tube and are also refered as Voight Pipes. By it's shape TQWT is a conical horn with relatively high cutoff frequency. The driver is not placed at the apex of a horn as usual but rather at 1/3 of horn's lenght. Nevertheless there is a degree of hornloading in lower midrange and upper bass. The TQWT therefore adapts well to fullrange or midbass drivers, which don't have very large excursion. Generally drivers somewhat between the extremes (around 0.4 Qt) seem to be ideal for these. Such drivers require some reinforcement in the lower mid/upper bass to counteract the baffle loss and hence benefit from the partial and slight horn loading provided. Proper mouth size should be 1-2.5x Sd depending of the author, which should be closed down a bit to get the best sound.
TQWT can't be seen only as a combination either helmholtz resonator or TL. It's behavior is a complex physics of 1/4 wave helmholtz resonator, bass reflex loading and horn loading. Therefore, TQWT cannot be successfully represented by only one of factors involved.
The port is used to adjust the rear flow according to the driver type, internal damping and desired response. The height of the port should also be adjusted through both measurements and listening sessions. System response will be primarily determined by the respective line-length and vent resonant frequencies; the driver position being used to create destructive interference of the higher frequency stuff we don't want coming out the vent (that is, it shouldn't be at an even fraction of the acoustic length of the pipe).
During the tune-up, it's a good idea not to close definitely a side of the box to allow easy modification of the internal damping.
The TQWT is really good at a few things. It manages very well to combine a horn and transmission line (and also some reflex loading). TQWT's TL behavior offers a nice acoustic load for the driver over most of it's operating range and in addition the bass reflex reinforcement can be tuned pretty low so that a pretty deep and tight bass can result.
The main problem of the TQWT is that it will produce a combfilter effect due to line resonances at lower frequencies, certain bass notes would be near inaudible, other would boom way too much, a very uneven and lumpy bass response. The only way to reduce these line resonances is to stuff the line severely, which changes air speed and therefore acts as prolongated line, but at the same time kills efficiency. The notches are caused by line harmonics cancelling the output from the drivers front. They correspond to impedance curve peaks which can be easily seen on a plot.
There is fortunately another option. Instead of troublesome tuning, two or more pipes can be employed in one enclosure, possibly even with different drivers. One pipe should be tuned exactly 1/2 octave below the other, once the minimal stuffing in the throat (the narrowes point in the tapered tube) is taken into account. The trick is to have a major port resonance at the lowest frequency desired (essentially the driver's resonance). The pipe resonance will likely be somewhat higher than that. The port then needs a second 'parasitic' (pipe type) resonance at the second harmonics of the line resonance. Normally this (2nd harmonic) resonance is out of phase with the driver's front radiation and hence creates a cancellation, the source of the deepest and lowest notch. This means the 'parasitic' and normally unwanted resonance of a classic port is desired. What it does is to simply remove energy from the pipe at the the 2nd harmonic. In any case, now one pipe will have a 'peak' wherever the other has a dip. If this is well calculated such enclosure will deal well with the resonanes, having a much flatter impedance curve and a fairly flat frequency response. This procedure should provide a deep and tight bass with a pretty even response.
There is a comprehensive study on TQWT with additional helmholz resonators writen by Jack Jakulis (Word 97 format).
Another possible improvement is use of multiple drivers placed at different positions along the length of the TQWT (SuperWhammodyne) to encrease efficiency and prevent cancelation problems with single driver TQWT. Check revisited edition of TQWT on Lowther Holland page, where another driver is added to cure uneven response of a single driver TQWT.
Stuffing Methods
Usually TQWT produces excesive midrange output. In order to lower it's output lining and stuffing must be used. There were many dicussions where this should be aplied.
One of the ways to reduce line resonances is to stuff the line severely, which 'elongates' (changed speed of sound) the line and prevents midrange output, but at the same time it decreases efficiency. This method is usually applied in transmission line designs, where theoretic principle derives from long lossy pipe.
Lining of the TQWT's sides is useful for prevention of reflections from side to side of expanding pipe (horn).
Instead of a smart talk, here are measurements of different stuffing strategies.
THE VOIGT PIPE
The Joke!
I made these as a joke one afternoon having picked up the drive units in Maplin, and from some scrap bits of ply. I didn't expect anything much from them - it was just an experiment to hear what a single full range unit would sound like. The JOKE was on me!!!!! To say that I was shocked would be an understatement but I went to bed dreaming of the music I had just heard.
The next few days brought further confirmation of them and they ran in and after a couple of week I suddenly realized that I was listening to more music that I have been of late. But it was the anticipation of listening when I was coming home every day that made me think of what was happening here. Weeks passed and I still was enjoying them like nothing before - they were bringing the magic back into the music. I was hearing more and more and the excitement was there - complete with the goosebumps!
Once you experience the full range driver you will never go back to crossovers and multi-way speakers. With such a high Fr, I was not expecting anything from the bass department - oh how wrong I was there too..I have no problem at all in this area, yes they are a bit bass light and there are times when you wish there was just a little bit more there - but that is more the exception than the rule.
Some magazine did a spectrum analysis of a piece of music many years ago and something like 85% of it is in the mid range..that being from 250 - 2K...so unless we can get this right then what on earth is the point of extended top or pant flapping bass? The mids are the essential and crucial part of what we hear and also the area where we are most sensitive. No wonder thoes multiway units that crossover right in the middle of that range seldom sound good.
The Voigt Pipe with its single full range driver is the most amazing speaker that I have heard. I had not realized just what Dynamics were before this, I did not know what it was like to experience the total integration of tweeter and mid in a crossoverless format. There is a 'Rightness' about the seamlessness of the sound.
Everyone that has heard them has been gob smacked at their performance ..without exception..They have a realism - that flesh and blood quality that is so elusive in most speakers. These are FUN. This is what its about..fun!
The Audax HT210A2 full range drive unit is a real bargain...i.e., cheapie! But that in NOT why I have it presented here. It is a 8' high efficiency driver of 94dB with an Fr of 55Hz and is an 7.6 Ohm unit and is good up to 16Khz. Cone material is doped paper and the wizzer is also what looks like some sort of treated paper - though stiffer.
Initially I thought they were a bit hard in the upper mid to top but after a few weeks that has totally gone and the slight shouty quality that I heard before has now gone altogether with the use of the 300B amp. This is indeed a marriage made in heaven. Driven with 8 watts they will blow the top off your house and their dynamics will slam you back against the wall with their speed. This is how real vocals sound. Common - forget about the great sound that you have and feel the music with the Pipes and get off the boring treadmill that you are on in the ever upgrading path in the hope of getting better sound and never being satisfied.
Ok, the vent/port you will see is not the usual that others have used. Normally this vent has a horizontal floor and is approx. half the height of the one here. Why? .. well by my way of reckoning this layout will divert the sound waves off the reflector base and out into the room better than one with its base horizontal in which case the sound waves are reflected back up the pipes adding to coloration and reducing control, because of the pressure wave acting against the down coming wave. The floor center point, from left to right is in the same position as the usual set-up..i.e. - imagine that you had pivoted the floor on its central axis between the two sides.
Only the upper section of the pipe above the driver, is lightly filled with acoustic damping whilst the area directly behind the driver is lined with 3/8' wool felt. Nothing at all in the lower section. After about six weeks of daily use I realized that they really need to be made properly, so the one that you see here are in fact the second pair and these are made of solid wood not ply or that horrible dreaded MDF. Sorry but I just refuse to use that material anymore - it just seems to rob the life out of the music. Any reservations that on me may have about them, and yes they are not perfect but what faults that do exist are benign in their presence. Sins of omission rather than addition as they say. But what they have in volumes is that immeasurable quotient of speed fun and dynamics and they do not suffer the sweet spot of many single drivers..hey you move around with these and still feel that you are having your cake and eating it too.
For so little outlay and so little trouble to make these have got to be worth trying out for yourself if for no other reason other than curiosity and keeping you entertained for the weekend.
Height = 76'
Width = 8.5'
Depth = 10'
Driver = Audax HT210A2
Efficiency = 94dB
Power Rating = 55W
Fr = 55Hz
Material = Unfinished Solid Pine
Dimensions are all internal
Ok, so you can get an idea of where to start with the stuffing..this is what I have done - but experiment yourself - there are no absolutes in this game and some may prefer the stuffing in the lower part of the line - indeed as one would find in a folder pipe.
The triangular void in the base is just begging to be filled with sand or lead shot, which apart from aiding sound quality will greatly help in the stability too.as it is rather unstable with its small footprint and height.
Also, if one does not initially fix the reflector plate,but makes it a tight fit - then there is the option of adjusting the angle and height of it to suit your preferences before finally fixing it permanently.
I have seen other versions of this pipe with the units mounted on the sloping side, rather than the vertical one and I have tried it with the cabinet aligned as such, but find that as you might expect - the sound is upward firing..great if you stand up while listening! Sorry, not for me.
The angle of the deflector? Well, I have made it at 45degrees to the meridian line through the Pipe, when viewed from the side, though the differences are not pronounced with a variance of a degree or two. Go try for yourself...
THE VOIGT PIPE
Where Do We Go From Here?
or..is there Life after pipes?
The original Pipe used a horizontal base, well and good but as you have seen I then tried the base plate at an angle to create a reflector. This was an improvement for me anyway..so how could I improve on this?. Well rather than bounce the sound at 45 degrees out into the room - it seemed like the logical progression to smooth this out and give a better transition into the room by means of a curved reflector. Lets face it, sound does not like flat angular surfaces and the curve has made a real big difference to both the bass quality and also to the mid range and imaging too.
This is further enhanced by the use of a light layer of wadding lining the curved section by cleaning the mid somewhat. I can only guess that any remaining sound waves that may have been reflected back up the Pipe are damped by this.
This is where not finally fixing the base piece into position is a great benefit for those wanting to experiment with different terminations. Guess you can get a better idea from this pickie.
The curve is made from Flexiply fixed to a former and is not at this stage actually fixed to the cabinet but is made just as a tight fit .. yeah .. as no doubt I will want to experiment further!!!!
cone mod Much has been said in the past about adding foam between the wizzer and the main cone...nothing new here... except I didn't use foam. i have found that it can rob too much of the top end so a similar but alternative solution was found with the use of polyfil teased out very lightly. This is then wrapped around the space between the two cones and with careful teasing and intertwining of the fibers through each other, can be made to stay in place. This is extremely light and I am of the opinion that the longer fibers in this are better at damping than multicell foam ( which will weight more also). Like so much in this hobby - less is more - to quote that often spoken cliche. It now appears that this unit is no longer available.I bought mine almost a year ago(1999) and didn't get around to using it until now..which is Sept.2000..but I have new spare ones available if anyone is interested
One thing I will say is the with the Pipes - the equilateral triangle set-up is a must and those of you thinking of firing them straight ahead down the room - well , look elsewhere..they just don't work in that way. In my situation the axis crosses about a foot in front of me. Placement within the room .. OK .. a matter for each situation and room , but in my case they are 34' from the back wall and 20' from the side wall. This is what works for me - that is all I can say!
Andy Rondeau's Do-It-Yourself (DIY) Speaker Project
I currently own a set of self-built DIY Voight Pipes. There are four traditional pipes used for both my front and surround speakers, and a modified pipe for my center channel. All five speakers use a single Radio-Shack 8' 35-Watt full-range driver. (40-1044) What follows are two pages, one describing my the construction and use of the five speakers, and the other describing my quest to magnetically shield the drivers so that they won't interfere with my television and cause data loss.
Overview
This page consists of a description of my Voight Pipes. The design used is based on Derek Walton's pipes. All five speakers use a Radio Shack 40-1044 driver, which is a 35-Watt, (70 max,) 8-inch full-range driver. They are made out of Pine, and use fiberglass insulation as filling. I magnetically shielded the drivers to prevent interference on my television screen.
I chose to build these speakers because they are electronically simple to build: There's no crossover!
The Story
I found the design in February of 2002 while co-oping in California, but I didn't have time to build them until I was back home in Massachusetts. During a school break, I constructed a single pair of pipes. The backs were hinged so that I could adjust stuffing, felt, etc. Once I was satisfied with the sound, I screwed the speakers shut.
After I graduated from WPI, I found the time to construct the remaining three pipes to make a complete surround-sound set. I adapted the design so that I could use it as a center speaker with the distinctive triangular peak that the other pipes contain.
The Design
Derek Walton has a set of plans with internal dimensions. My challenge was adapting these designs to work with pine that is 0.75 inches thick. You may view my design notes here: (Although, they are not neat)
requirements.pdf
angles and math.pdf
For the center speaker, I chose to twist the pipe to the left under the driver, and then behind and back to the front. (This is the approach used in the Bose Wave Radio.) To do this, I redesigned the bottom to have the same volume and a different shape. You may also view my notes and calculations, but these are worse then the ones above!
p1.pdf
p2.pdf
p3.pdf
Material Choice
The materials used in the project were chosen for practical purposes. The first pair that I built were experimental, and I had no desire to invest any more money and time then needed. While I could argue that full-range drivers have better imaging then traditional multi-way systems, and no crossover distortion; the real reason that I chose the Radio Shack 40-1044s was to save money and keep the design simple. The full-range drivers are much more economical because there is only one electronic component per speaker to purchase instead of a minimum of three.
I chose pine because of its appearance, price, and simplicity. More experienced DIYers will tend to build their speakers out of a material that is 'better' acoustically, and then laminate or paint the cabinets to their liking. I wanted a material that was ready available at Home Depot and would still be eye-pleasing with minimal effort and expense. The same theory was applied to the stuffing; fiberglass insulation is cheap and available at Home Depot.
Complications
At first, I stripped the wood using a handheld circular saw. Big Mistake! The angle on the side pieces for the back was hard to cut, even when I later used my neighbor's table saw. When I sealed the boxes for the first time, many screws did not go in straight and occasionally popped out on the surface of the pipes. (For the later pipes I used a drill guide.) Some calculations for the center channel were inaccurate. Also, not all of the center channel goes through a properly-angled pipe.
Results
These are the best-sounding speakers I've owned, every recording comes to life! The speakers are much clearer then inferior multi-driver units with vocals. Due to the single driver, they are lacking a bit in bass and treble, however, this is easily fixed with a little bit of equalization, or bass management at louder levels. At 35 watts, 70 max, they are loud enough, (more then 100 decibels,) for a typical room. For ordinary stereo, they have the best imaging that I've ever heard.
These speakers are ideal for flat, realistic playback and volume. People who like to over-emphasize base or treble will find them lacking. (Have you ever listened to someone's radio and realized that things just don't have that much base or tweeting in real life?) Likewise, those who plan to prefer to listen at painful levels may wish to look elsewhere. The 40-1044s' range is perfect for vinyl, CD, and movies, but they are a bit lacking when it comes to using them with DVD-Audio. (I haven't tried them with SACD.) I'd like to add a super-tweeter to pick up notes above 18,000 Hz off of high-resolution recordings.
I'm still inconclusive about the center channel. Occasionally, I hear it resonating at lower notes, which is undesirable. Maybe in the future, I might rebuild it as a television stand, which would allow for the tube to follow the original plan much more closely. (Unfortunately, this approach would prevent me from buying rear-projection televisions.) Another problem with the center channel is that it requires a high ceiling or a lower television stand, because of the point.
Pictures
All Five speakers
Conclusion
Based on my experience with these speakers, any speakers that I seriously invest in will probably be based on full-range or extended-range drivers. I may add bases to the bottom, as they tend to be a bit wobbly. The center channel proved to be an awkward design at best, and thus when I have more time and money I might re-build it as a combination speaker and television stand.
Voigt Pipe Project
C.Joye 6/01
Voigt pipes were a creation of P.G.A.H. Voigt in the 1930's which are similar to the concept of a transmission line, except the speaker is placed near the center of the horn-shaped pipe. Since this is intended to be a full-range, single speaker sound source, the type of speaker chosen is rather critical. One of the favorites is the Radio Shack #40-1354A, a very versatile driver that had a whizzer cone to aid the high frequencies, and good overall tonal balance for a mere $10 -- until they discontinued it. Some very excellent Voigt pipes were constructed for well under $50. The triangular nature of the Voigt pipe causes its resonant frequencies to be spread across the midrange bands, and the length of the pipe accentuates the bass frequencies very well. Because of this, the Voigt pipe can produce a very wide frequency range with very natural tonal balance.

After deciding that I needed some speakers in my basement (I had 12 tube amplifiers, an ancient pair of cheap two-way speakers with one woofer that literally melted when a 6550 failed, and a test pair of little 6.5' speaker boxes!), I decided that the Voigt pipe would be the way to go. I had my eye (but not my wallet) on a pair of $2400, polished aluminum D2-al2's from O'heocha Design, but decided to build a simple Voigt pipe instead. I already had two 5' drivers that I hoped would do the job. They are not full range drivers and I have no idea what their Qts is. They don't have great high frequency extension, but I didn't mind because I wanted to use my plasma tweeters for the highs. They do have awesome low frequency characteristic that I hoped the Voigt pipe would bring out.
I went to Home Depot and got a very nice sheet of 3/4' Birch Hardwood plywood for $42. I was bent on building both pipes from one sheet, so mine are only 7.5' wide and 9.5' deep (I wanted to preserve the 7 degree angle that Jeschke used). They stand ~74' tall at the moment (with the bottom attached) and I located the speaker center at 39' above the floor. I used liquid nails and tub caulk to glue and seal the boxes, with a few nails in the back panel.
I put a few nails inside the pipe to hold the stuffing in there. I bought a 5lb bag of Acousta Stuf from Parts Express, as well as some gold binding posts.
I used ~1.2 lbs of stuffing per pipe in the upper half.
The sound was surprisingly good for a pair of midbasses. The high frequency extension was a little weak, but thats what my plasma tweeters are for. The midrange was very full and clean, and the bass was strong down to about 50Hz. I heard details in music I had never heard before. The biggest problem was doppler distortion at high volume levels (~95dB) due to the excessively heavy cone. It makes trumpets sound a little like they are under water when a large bass note hits (like the Olympic Fanfare, Starwars theme, Star Trek theme from the Telarc CD I used). The cure would be for me to get a subwoofer. I have my eye on a Pheonix Gold Cyclone Sub, which is made for car audio, but is the most bizzare speaker I have ever seen (it looks like a washing machine agitator, and works like an Archemedian screw compressor).
I have been listening to these for several hours now and they sound really really good with the plasma tweeters. The midrange definition and presence is amazing. The bass doesn't quite come out and grab you, but it's definetely there, and very accurate and well-defined. I need a sub for the lower frequencies. I want to listen to them all day and night. I have gotten used to the level of bass they produce: I think it's not that they are weak, but that I am used to listening to bass a few dB louder than it should be in my car (need to combat road and wind noise by increasing bass). I think these pipes are the best sounding speakers I have heard for under $100, and my friend says they sound better than most big 3-way speakers he's heard. I love the single-speaker wide-bandwidth sound now. The fast transient response of such wide-bandwidth systems just makes the sound so smooth, like a well built horn-loaded speaker. My system diagram.
Parts List:
4'x8' (3/4' thickness) Birch hardwood sheet (around A-B grade): $42.00, Home Depot
Two 5.25' midbasses, 50W each: $8.00 (clearance), Parts Express
Two sets of Gold binding posts: ~$2 each, Parts Express
2.4lbs of Acousta Stuf: ~$15, Parts Express
7 feet of 2x14gauge copper speaker wire: ~$4 Parts Express
Half-tube of Liquid Nails: ~$1, Hardware store
Half-tube of Alex Plus caulk: ~$1, Hardware store
Two piece of Dynamat: ~$2, Parts Express
Eight self-stick rubber feet: ~$3, Radio Shack
Total estimate: $85.00
Obviously, the wood was my biggest expense. If you happen to have a pair of good cheap speakers, like the RS 40-1354a, enough scrap wood, and an old wool blanket, there's no reason you couldn't build an excellent Voigt pipe for less than $20.
What's next? I want to get a subwoofer so I can high-pass filter the Voigt pipes around 60Hz. I don't think I'll low-pass filter the Voigt pipes, they cut off pretty naturally around 3kHz with these 'heavy-coned' speakers (their cones are not really heavy at all, in fact they're probably lighter than most midrange cones. They are just a bit too heavy for pure full-range sound). I think I will build another pair since I'm so pleased with these, but this time using a Lowther driver, or Lothx driver because a very light cone is very important (but they typically cost $300 each!!). I would like to try the folded Voigt pipe and would like to make them longer so I can used them without a sub. I may try making one three-sided with all sides being triangular (different-sized triangles?).
The Equations I found for Voigt pipes seem to match up well with my version (see right). I think these equations are for a fully stuffed pipe, because mine seems to drop off around 55Hz, and it's about 60% stuffed.
Adventure with Voigt Pipes
by Herbert Jeschke
For some time I was already tired of our stereo, I really did not use it much, but my daughter did and I liked what she listened to, only I could hardly stand the speakers threshing out the same bass-note when it got below 100 Hz somewhere. Surfing the inter-net for speaker projects, I looked at many but shied away from complicated vented boxes, transmission lines and crossovers with associated math. When I found the design of the Voigt Pipe at the site of the Lowther Club of Norway I was taken by the simplicity of it and the fact that it uses a single driver, much like a point source that would mirror the microphone that originally recorded the music of acoustical instruments. It also places the driver at ear-level of a sitting person placing the listener on a par with the performers.
I didn't know how I would adapt to the steep price for Lowther drivers but went ahead anyway and build the Voigt Pipe cabinets thinking I might try some other full-range 8' drivers meanwhile. I used 3/4' chipboard that I had left over from a sub-flooring job. Along came summer 1999 and time passed with other predilections. In September came VALVE e-zine #4 with a glowing article about a small vented bookshelf speaker that used the Radio Shack #40-1354 drivers all of 5-1/2' big and famed them for their outstanding mid-frequency response. The article also said that the hardest material like cultured marble would be best for the boxes so I went out and got some 8' x 8' x 24' chimney tile (flue liner) and wanted to cut round holes in the sides of it. I have not found a good way to do it until today.
Frustrated by that I still wanted to try these little 5-1/2 inchers when my eyes fell on the Voigt Pipes in a farther corner of my shop waiting a better day. The Pipes already had their 8' holes so I had to make a baffle to bridge the difference. Since it is a good idea to place the speakers off center in a baffle and because the scrap plywood I had offered that shape I made those baffles looking a little like wings pointing toward the middle of the sound stage. I thought that might help to fill in the void I sometimes sense in the middle of a stereo pair too far apart. That done using the fast method I hooked them to a stereo in my shop. The sound was stunning, I mean immediately better than anything I have listened to since the Triode Show in spring 1998. I got my wife to come down and put her in the chair at the sweet spot. She marveled and told me how you just know right away when you listen to some real good equipment. I did not change anything in 4 weeks. The Voigt Pipes are allowed in the living room now in spite of their unfinished surfaces and we enjoy them. They have 3 dimensionality and depth even when we are far away from the sweet spot. Midrange is just great and low end is amazing - probably due to the Voigt Pipe design, a horn design married to a transmission line. The RS drivers put out a lot. I need only 1 to 2 watt for loud listening levels on classical music. The cabinets might seem big to some but really they are only tall and take a square foot of floor. It is good to stand them a step away from any wall or more. They are good for fairly large rooms where you can spread them 8 to 10 foot apart and 3 foot away from the wall or more.
Come December I build these little box speakers from VALVE #4 for my daughter to take to her dorm at college. I used just chipboard again but kept very close to the design given in the VALVE e-zine. That includes a pressure screw from the rear of the cabinet against the backside of the driver magnet. After Christmas we set up a shoot out between the speaker pairs, the Voigt Pipes and the Hawaii 5.0 boxes. The boxes sounded great, very fast and accurate, clear and happy without discoloration that I could hear. But somewhat the sound stage was attached to the speakers or not really free of it.
The Voigt Pipes let it all out, loose and open almost boastful, creating with ease the impression of the hall the music was recorded in. Both sets were driven by the same amp using its A/B switches. The Voigt Pipes are significantly more efficient and the bass is almost unbelievable thunderous and follows the played tone accurate without preferring certain resonances. I did feel however that the Voigt Pipe would benefit from the same pressure screw arrangement as found in the box design and after installation we noted improvement of control in the low frequency end. Some day I might carefully add a little tweeter using a film cap to couple it in, just to see if I really miss it. The RS 40-1354 are said to go up to 15 kHz but not much further and I like the absence of that abrasive hiss some tweeters offer from digital recordings.
Radio Shack SPECIFICATIONS for 5-1/4' HiFi Auto Speaker Cat. No. 40-1354A
Impedance 8 Ohms
Frequency response 50 - 14,000 Hz
Free air resonance 50 Hz
Efficiency (SPL at 1 Watt, 1 Meter) 90 dB
Nominal power 20 Watt
Maximum power 40 Watt
Magnet weight 10 oz
Speaker weight 30.6 oz
SPECIFICATIONS posted on Bottlehead Forum by Greg on 1.20.2000
' Fs = 71.5 Vas = 7.3 liters Qts = .49 Qms = 3.85 and he notes: These should be enough to get you started. They seem to indicate a 14 liter ( .5 cu ft) box tuned to about 58 Hz. Good luck ' Thank you for the posting Greg!
Hints For Builders:
from the Lowther Club of Norway: (partial quote)
'The Voigt Pipe: The world's most easy-to-build High End Loudspeaker' A visually appealing speaker with good bass response down to 40 Hz. High sensitivity / efficiency. The Voigt Pipe acts as a cross between a horn and a transmission line. By tapering the pipe as shown, the resonances will spread over a wide range of frequencies. The Voigt Pipe is yet another of the late P.G.A.H. Voigt's audio inventions.
Loosely stuff the upper half of the pipe with clean, long hair wool or equivalent damping material. The midrange can be tuned somewhat by experimenting with additional damping directly behind the driver. Dimensions are internal! Use 3/4' ply or MDF. Use Lowther drivers PM 6A, PM6C, PM7A.
My drawing of the Voigt Pipe with dimensions in inches:
When I built the Voigt Pipes I used good grade 3/4' chipboard, but now that I found out how well this design performs I must recommend a good grade plywood. I will build the next ones for a friend of 3/4' Baltic birch ply. The cabinet does vibrate and works as a secondary radiator to some extend, similar to a musical instrument.
Look at the drawing with me.
ALL DIMENSIONS ARE INTERNALLY MEASURED!
The basic shape is a long wedge that stands on its smallest side. The front side is vertical, rectangular and carries the speaker's round hole and the rectangular vent hole in the bottom. CUT THESE HOLES AFTER ASSEMBLY!
Only the side pieces are tapered or actually one rectangle cut diagonally into two triangles. Make these triangles first, that is your trickiest cut. Start with a rectangular piece of your wood 8-3/4' wide and at least 76' long, better longer if the cut should go wrong. Lay out the triangles on that board in such a way that your diagonal cut starts an inch or two away from one end of the board. You want to end up with the 8-3/4' by 71' triangle but cut the short rectangular crosscut after the diagonal cut is satisfactory. Clamp or nail the triangles together like a sandwich and plane or sand the triangles together so they end up having exact the same dimensions when taken apart again. Careful with the thin ends of the triangles!
The rest is easy. The front panel is 8-3/4' plus twice the thickness of the triangle wide. It is 71' long unless you have to accommodate a slightly different dimension to fit your triangles. The back panel is as wide as the front panel but longer like 71-5/8', but it doesn't hurt to make it even an inch longer because it can be cut flush with the front panel at the top after assembly. The bottom plate butts against the four previous panels. It is square 8-3/4' plus twice material thickness by 8-3/4' plus twice the material thickness. The back panel should be miter-cut to fit the 7 degree angle with which it meets the bottom plate but I left it square cut and filled in the gap with silicon caulking. You will need silicon caulking at the top as well where the front and back meet at a sharp angle. When the glue is set and dry, cut the holes in the vertical front panel. NOTE the 7-7/8' by 4-7/8' vent-hole is not flush with the bottom but 3/8' higher than the inner bottom!
If you have children, mount the speakers on a slap of stone or marble about two foot square to keep them from falling over easy. Do not put legs on the bottom of the speaker cabinets, because the rectangular vent hole uses the room's floor for extended bass radiation.
The Pressure Screw
This can be put in after you have already listened to your new speakers, but I found it audibly to great advantage. This is of course true because I used the RS drivers that have pressed steel bodies. Lowther drivers are likely to be rigid enough not to need that extra bracing. Same is probably true if you use cast frame speakers.
I used 3/8' threaded rod for the screw and cut it to proper length after trying it in place. Drill a 1/2' hole behind the speaker through the back panel. It should be vertical to the front panel and coincide with the speaker axis. Take about a foot of 2' by 3' lumber and slice it in two pieces lengthwise but at an 7 degree angle. Cut each sliced piece 8-3/4' or a little less long. That braces the rear panel across its width and will carry the T-nut for the screw. Cut a 2' by 2' by 1-1/2' block and drill a 1/2' hole in its middle but only 2/3 into its thickness. Glue that and center it onto the rear of the speaker magnet. I used Silicon glue for that. Loosely assemble the whole pressure screw jig and find out the screw length you need. Cut it with a hacksaw and cut a slot for the screw driver in the outer end. Fix the speaker well into its hole now and then turn the pressure screw against the magnet with some feeling and judgment. Not too hard but hard enough to withstand all expected vibrations. It works like the sound-post in a violin and helps keeping the magnet rigidly mounted.
Let me reiterate: The wings and the pressure screw plus the RS 40-1354 drivers are the only things that I added to the standard Voigt Pipe design from the site of the Lowther Club of Norway. Below the 'Wings' which I call baffle is the standard 8' diameter hole for a 8' Lowther driver. It is beveled toward the inside because sound doesn't like sharp edges. On top of the 8' hole is the wing-shaped baffle: basically a rectangle 14-1/4 inch wide by 10-3/4 inch tall by 7/8 inch thick in my case. One of the vertical sides coincides with the vertical edge of the Voigt pipe. The driver is mounted in a 5-1/4 inch hole (beveled inside) which centers around a point 4-3/8 inch from the top edge of the baffle and 5-1/8 inch from the edge of the Voigt pipe, which coincides with the vertical centerline of the front of the Voigt pipe. The bottom edge of the rectangle farthest away from the driver is cut away in a gentle sloping curve tangential to the far vertical and to the bottom edge of the rectangle. I drew that curve by hand on one baffle and copied over to the other baffle. If you have difficulty with that shape take a piece of spring steel wire and bend it in a curve that touches the sides of the rectangle in a gentle slope almost coinciding with the sides near the corners. Hold it there and let your partner draw a line along the steel wire. I don't really think there is much to it and it would probably not sound much different with just a plain rectangle or whatever design you like. The baffle and speaker is mounted with drywall screws and sealed with latex caulk, the household kind.
Currently I run my recently-built single ended triode amps (Svetlana 811-10) with my Voigt Pipes and really deem myself lucky to have arrived at a really good sounding system so easily.
My professional past: Audio engineer for German TV and Film, Carpentry contractor, cabinet maker, audio engineer for archival recording in Philadelphia.
Wishing you much fun building and enjoy the music. Happy listening! - Herbert Jeschke
A Straight ML TQWT
by Bob Brines
All photoshop plugins. Free download photoshop dress remove in Files at Software Informer.
The Straight Pipe
This project was conceived as a response to the Voigt Pipe found elsewhere. It is a straight pipe based on Martin King's Mass-Loaded TQWT technique. Designed specifically for the Radio Shack 40-1354a (unfortunately out of print) wide-range driver, it should accept any 5 1/4' driver with a fs of 50-60 and moderate Qts (0.3 - 0.5). For a larger driver with the same fs, scale up the cross-section by the Sd of the driver.
The internal dimensions are determined so that the throat area is equal to the driver Sd and the mouth area equal to 4 times Sd. I think that this produces the best compromise between increased horn loading at f3 and the straightest curve between F1 and F5. The depth is increased by 1/2' to allow for the vinyl tile used as internal damping.
The cabinet is built of 3/4'x12'x6' MDF shelving. To damp the cabinet, all internal surfaces are covered with vinyl tile glued down with vinyl mastic. To damp any reflections back through the driver, a 6' x 12' pad of 1/2' yellow Fiberglas® is placed directly behind the driver. Finally, the cabinet is lightly stuffed with polyfill, from the top down to just below the level of the driver.
One can argue that this design could use some bracing. I don't think that bracing is warranted because of the modest SPL levels expected. If you must, I would suggest asymmetrical stiffeners on the four main panels. I have no idea what havoc shelf braces would bring.
Modeled SPL after stuffing:
Port output (blue) and driver output after stuffing:
Construction Details
These instructions are intended for a novice who has never attempted this kind of construction. It is overly detailed for anyone even modestly familiar with speaker building, but someone might benefit for the details.
This project is designed to be built with hand tools using three 3/4'x12'x6' MDF shelves each cabinet. The cabinet is constructed entirely of butt joints. Miter, dado and tongue and groove joints are just not realistic with hand tools. (There is a tool called a dado plane which can be used to.. Forget it!) Therefore, the panel layout is arranged to make maximum use of the factory edges of the MDF shelving for the glue joints. Only the back panel needs to be finished on two edges.
The panels are glued and screwed with yellow PVA glue and 1 1/4' coarse-thread drywall screws. Screws are run through the face of the MDF panels into the edge of the joining panels. Screws into the edge of MDF provide no real mechanical strength. They are adequate to provide pressure to the joint while the glue sets, but that's all. After the glue sets, I remove the screws and plug the holes with light-weight spackling. To assure proper pull-up of the joints and to prevent splitting, drill 5/64' pilot holes the full depth of the screw, and then drill 1/8' clearance all the way through the panel. I put screws on 6' centers.
The Back Panel
Mark the width of the back and draw a cut line the length of the board. Cut the back to width, leaving enough material for finishing. Put the cut off piece between two new shelves, square the edges and clamp both ends. Put the back between the shelves, align the cut line with the top edge of one of the shelves and clamp both ends. Plane the back down flush with the shelves. It is critical to the final fit that the planed edge be straight and square. Cut the back to length plus 1/4' extra. Save the scrap piece. It will be used for the port block, and as a spacer during gluing.
Drum Library Vol 1 Zipper Pencil It is also known as wet- blue for its color derived from the chromium. More exotic colors are possible when using chrome tanning. R&B Drums Exclusive Heat vol.1. 1.94 MB ZIP File - Platform. This Library is compatible with all pro gear including the Roland. Contains 1.8 GB of well organized acoustic drum samples. Drum library vol 1 zippered download. Drum Library Vol 11 PAUL NICE. 5.0 out of 5 stars 2. Drum Library: The Lost Volumes VARIOUS ARTISTS. Drum Library - Volume 7 PAUL NICE. 5.0 out of 5 stars 1. Czarface Meets Metal Face Czarface. 4.8 out of 5 stars 28.
Truing the back panel:
The Baffle Board
Cut the baffle to length with a little left over for finishing at the top. Cut the width with a little left over at both sides. Draw two construction lines marking the outside edges of the side panels. These lines are critical -- get them right. Mark this side 'Inside'. Make the driver cutout . Finally, put a 3/4' round-over on the outside bottom edge.
The Side Panels
Cut the sides from a single piece of shelving. Mark the length of a side, The mark the top and bottom width and draw a cut line. Continue the cut line the full length of the board. Flip the board end for end and repeat the procedure. Saw the sides out, leaving enough material for finishing. Cut off the tops, leaving a little material for finishing. NOTE: You now have two panels with the cut line draw on the inside of one and the outside of the other. Pick one panel and mark the cut line on the opposite side. Draw a line 1' up from the bottom on each panel for alignment of the baffle.
Assembly
NOTE: The baffle is glued to the rest of the cabinet AFTER the cabinets is lined and stuffed.
Screw the cabinet together. Don't even think of going for the glue bottle until everything dry-fits together properly. Place the baffle on your work bench inside up. Stand the side panels up on the baffle. Place that piece of scrap you saved from cutting the back panel :-) between the sides near the bottom. This will assure that everything will be square. Align the 1' lines on the sides with the bottom of the baffle and clamp the sides to the scrap with a bar clamp. Now the same procedure at the other end. Use the port block as a spacer between the side for alignment. Place the port block between the sides and clamp the sides with a bar clamp. Check that everything is lined up -- the sides are on the construction lines on the baffle and the 1' lines line up with the bottom of the baffle. Check it again! Slide the back panel between the sides. Support the back at the cut lines on the sides with C-clamps. Align the inside edge of the back with the bottom of the sides. Drill and set the first screw at the bottom and the last screw at the top. Gently roll the side-back-scrap assembly on its side. Check the alignment of the back and side at the middle. Drill and set the middle screw. Now drill and set the rest of the screws on this edge. Flip the assembly over and set the rest of the screws on the other edge of the back.
Once the back and sides are screwed together, you can remove all of the clamps. Place the cabinet on its back and screw down the baffle. No more admonitions to check the alignment. Once you are sure everything fits together properly, place the cabinet on its side, remove the side facing up. Sand down any material raised around the screw hole to help make the joint tight. Run a 1/4 bead of glue down the edge of the back. Spread it with a finger, making sure the entire edge is wet. Replace the side and screw it down. Flip the cabinet over and repeat with the other side.
Once the glue sets, plane the bottom of the back flush with the sides, and plane all four panels at the top down to the cut marks. Cut a piece of MDF for the top, glue and screw it to the sides and back only. Screw it to the baffle for alignment, but try to keep glue out of the top/baffle joint at this time.
Damping
I decided to line the cabined with vinyl tile to quiet the panels. I bought some (20!) 12' x 12' vinyl floor tiles. I cut them to to fit on all four sides of the cabinet. Mask all of the edges and the baffle that will be glued later. This is important! Now apply vinyl floor mastic to the insides of the cabinet (and the baffle) with a notched trowel. Set the tiles and let the whole thing set overnight. I am not sold on the need for panel damping in a low power speaker, but it can't hurt.
Lining and Stuffing:
(Since I've done all of the work, you can go to the bottom of this section and install the recommended stuffing.)
Make the piece for the top of the port. I tried several lengths (ok, widths) during the stuffing trials. 6 1/2' x 3' is the best size. Put a 3/4' round-over on one long edge. This piece is wedged in place during trials.
First, I took some SPL measurements of the bare pipe. The black line is the combined output, the red line is the driver output and the blue line is the port output. Below that is the modeled combined output.
Very good! Other than the peaks on the spikes are rounded over, the correspondence is almost exact.
Next, I lined all four sides of the cabinet with yellow Fiberglas®. The results are:
It's over-damped! I'm going to have to remove some of the lining and retest.
Ok. Removed all of the Fiberglas® except for a 6' x 12' piece directly behind the driver. I played with several diferent packing densities and tried both Miraflex® and polyfill. The bottom line is Miraflex® and polyfill are one-for-one replaceable. Also, packing density is not critical, within reason.
However, it is EXTREMELY important that the stuffing does not extend more than 2' below the driver, or bass extension is rapidly lost. The final stuffing configuration is moderately firmly pack polyfill (simply because I tried the Miraflex® first, and there is no need to change back), from the top to 2' below the driver:
Final Assembly
Glue and screw the baffle to the sides and top. Glue in the port piece. Screws are not necessary, but make sure the fit is air tight.
(I put a 3/4' round-over on all edges of the cabinet. This is pretty much for cosmetics only, so put what ever edge treatment you want. However, do the edge treatment BEFORE you proceed!)
Build the plinth for the bottom. I decided on two thicknesses of MDF, cut as per the drawing. Glue and screw the one piece of MDF to the bottom of the pipe, then glue and screw the second piece of MDF to the first. True edges and apply the edge treatment of you choice. I put a 1/2' chamfer on the edges, just because.
The cabinet is now complete. Mount the driver, the input cup or binding posts, wire it up and give it a listen. Nice, no?
Finishing
Apply the finish of your choice. Veneer it, paint it, whatever. I'm going to do a black gloss finish. Not having any experience with finishing MDF, this part of the project turned into a real adventure.
The single biggest mistake I made was to try to apply primer with a brush. Two things happen. One, you get too much primer around the base and port. Also, the primer will not level, so there will be massive brush marks in the dried primer. Second, because of one above, it takes forever for the primer to dry, and don't think about sanding until the primer is really dry. Then, you need to sand virtually all of the primer off, which takes forever and clogs all of your sandpaper, because you didn't let it dry long enough.
Get primer in spray cans! Just make sure it is wood primer. Metal primer will be worse than useless. Put a couple of light coats on the raw edges of the panels. If there are any visible imperfections, fill them NOW with light weight spackling. Sand it off (150 grit) and apply some more. Repeat until there are no more imperfections, using 220 grit paper. Spray the entire cabinet with primer. Fill, sand, spray, repeat. Once everything is smooth, spray the entire cabinet and sand smooth with 320 grit. Spray the color coat. you're done.
Pipes in the paint shop:
Baffle Step Correction
These pipes, like all tall, thin cabinets suffers suffers from baffle step loss. In the far field, frequencies below 800hz are reduced by several db's. This makes the speaker sound thin, with little bass. One solution is to place the speakers flush against the back wall. This sort-of works, but is not good for imaging. The best solution is to install a baffle step correction circuit. Put a zobel (6.8uF cap in series with 8ohm resistor) in parallel with the driver. Put a 1.5mH iron core inductor in parallel with a 5 ohm resistor in series with driver. Adjust the value of this resistor to balance the sound of the speaker.
Another Voigt Pipe - with the Fostex FE207
by Dan Dicker
OK, so I'm bumming around the NY Noise show for 2002, nothing to show this year so I'm just another spectator. But, as usual, I meet the most terrific people at these events, whether I'm an exhibitor or not...so....besides the usual cast of characters, I come across Mr. Jonathan Weiss, who has brought a pair of Voigt pipes using a vintage 800ohm driver. Hmmmm, I think, this looks interesting.
I'd already done a pair of Diatone P-610's in the de rigueur vented box and found them to be wonderful, but I had since moved on to other, larger projects and had sold the Diatones. Yet, I could not forget the coherence of the single point source and the great ability of Full range drivers to disappear completely. Add to that the fact that my basement seemed to be filling up over the past few years with completed amp projects the COMBINED power of which couldn't light up a small cell: I now have 2 under 6W amplifiers and 2 more which can put out 15 Watts....downhill....with the wind at their back.
Needless to say, I've been looking for a simple, high-sensitivity, low anxiety full range project for quite a while since foolishly selling the Diatones, and after speaking to Jonathan, was convinced that the Voigt pipe might be a good way to go. Well, before embarking on this project I hit the internet, and found a wealth of information it would be silly of me to repeat here. The write-ups elsewhere in this DIY section will give you everything I had or anyone should need to complete this really simple project. I used Herb Jeschke's dimensions and found them to be spot on, and his advice about construction really useful....follow it. The only thing that I did differently is in the cutting of the rectangular port on the bottom of the pipe; I left out the 3/8' lip on the bottom, and installed a 3/4' base instead. A little easier to construct and more stable too.
Let me add just those few points that I think might be slightly original and worthwhile:
Driver selection: No great mathematical reasoning on these theories but this was my take. You want as smooth a frequency response as you can get, right? You know that the Voigt pipe's main issue is a lumpy response in the lower registers, a lumpiness that can be somewhat 'tamed' by stuffing the pipe. The stuffing will, however, reduce the sensitivity of the speaker, but compromises must be made, yes?
So, this was the 'magic' driver I sought:
A driver with a high (93db+) sensitivity, Qts in the neighborhood 0.2-0.3 to be a candidate for horn loading, as flat a frequency response as possible to find, particularly in the midrange, as high a nominal impedance as could be found, Alnico magnet a plus, but, here's the MOST important part...... I wanted the driver to have a response difference between its resonance frequency (Fo) and its midrange sensitivity to be NO MORE than 10db. In other words, when I looked at the frequency response graph, if the sensitivity of the driver was 95db/w, I wanted the response at around 50Hz to be no less than 85db. Why? I figured that the pipe could augment the bass response only so much, and I would have to reduce the midrange response somewhat anyway by 'hardstuffing' the pipe and flattening the 'humps'. If you'll look at the T/S parameters and response graph for the Fostex FE207 (available at Madisound), you'll see that it meets my needs perfectly. ALSO NOTICE, that some more expensive drivers do not meet these criteria quite as well, including the FE208 Sigma, or even the new-fangled, just out FE207E.
SO... look for a driver with a more gradual rolloff to F(o), and sacrifice a few db of sensitivity for a whole lot more balanced response, OK??? I have since tried quite a few 8' drivers in the baffle of the pipes, and it seems that my intuitive guesses have turned out to be useful ones. Other drivers have been inferior to the FE207.
Stuffing: As you might have guessed, I used more than the standard amount of stuffing. This won't hurt your wallet, however.... fiberfil stuffing, available at any fabric or crafts store, should run you about $2 / lb. I used about a l ½ lbs. Per box, including behind the driver. My point is, don't be afraid of using too much, you can only hurt sensitivity, which shouldn't matter too much, unless your one of those guys with the 250mW spud amps. I can run my pipes to QUITE respectable levels with my SE 2A3 amps, which are good for about 2 Watts and I don't even bother with a preamp and its added gain.......
OK, now let's cut to the chase. Total construction time....about 1 weekend start to finish. Total construction costs......about $300 including drivers, less if you use lauan or MDF instead of birch ply as I did....I 'splurged' for the extra $40, and also bought a pint of stain too...wow..big spender.
In terms of sonics, I put these pipes against my reference speakers and......they very easily held their own. Of course, they do the transparency and disappearing act that all full range drivers do singularly well and, although not as extended on either end as my references, they were really, really natural and open sounding. If memory serves me, they are superior to the Diatones I built by a fair margin, although both speakers shared many of the same advantages, the pipes being much better in the bass and throwing a much larger stage.
Build 'em..... you'll love 'em......
My thanks to Jonathan Weiss for the great suggestions and my great friend Ron VanTongeren, who had all the neato tools (rotozip, nail gun, monster clamps) to make assembly a 1 hour operation, as opposed to 10 hour ordeal.
Fred300B
94dB efficiency Voigt Pipes featuring Fostex FE166E drivers, with styling features inspired by the Cain & Cain Abby. These speakers offer surprisingly good bass down to 60 hz and a very coherent soundstage. They sound especially good driven by a pair of Bottlehead Paramour 2A3 amps. They can be built of Baltic birch veneer plywood with mdf trim, as shown here, for less than $250.
The Voigt pipes stand 72' tall and use Fostex FE166E drivers. These are the same drivers used in the Cain & Cain Abby, which inspired the cosmetic finishing.
These are the plans for a pair of Voigt pipes built by Herbert Jeschke, taken from the single driver website at:
http://www.melhuish.org/audio/DIYTQ4.html
the Voigt Pipe is a Tapered Quarter Wave Pipe enclosure, which is a very old design and not very popular today becasue of its size (if built full length like this one) or the complexity of the cabinet if built as a folded horn. But it's one of the easiest speakers to build if built full length like this.
You begin with two 4' by 8' sheets of mdf or plywood. I chose Baltic birch veneer plywood becasue my friend Paul and I built his Hammer Dynamics enclosures from this material, and the plywood is very attractive with just a coat of varnish. I had built a pair of pipes before using Radio Shack drivers and mdf, which are less expensive, but they didn't look or sound very good so I gave them away.
First you rip the sheet to make it more managable. Leave the remaining sheet a few inches longer than the 71' length for reasons I'll explain later. Then you rip the boards to the desired width. Each enclosure is built from only three boards: the front, the back, and the sides which are split from one rectangular board.
It's surprisingly easy to get two identical triangles from one board. I used another board as a guide for the handsaw. cut along the line, then drew the shape of the first side on the remaining part of the board.
I used some sophisticated tools cause I have them, but all the cutting for this project can be done with an inexpensive circular saw ($40 at Home Depot). Those little battery powered saws are useful for small jobs like this, but their endurance is about one cut, then you have to recharge.
Here's one completed side sitting atop the remaining piece. This is why you start with an overlength board. After you have cut one, you just lay it over the other and cut the bottom of the second triangular board to produce two identical sides. Be very careful handling the sides before the cabinet is assembled; the pointed tops are very fragile.
I don't want any visible screws so I'm using 3/4' stringers to glue the sides to the front and back. Here's the front with the stringers clamped and glued. The next step will be to cut the driver and port holes when the Fostex FE166E drivers arrive.
Finally the 6.5' Fostex FE166E drivers arrived, so I can do the driver cutouts next week.
Each enclosure receives three coats of fast drying semi gloss polyurethane varnish from a spray can. To get a smooth furniture finish the varnished cabinet must sit for 72 hours, after which I will lightly sand it with #220 paper and apply one final coat.
One completed enclosure minus its base, standing beside a Magepan 1.6QR for size comparison. This is a very easy enclosure to build. It could be done with a simple handsaw, a scrollsaw for the cutouts, and a drill.
Each speaker base is a 14X14 piece of 3/4' mdf. I rounded the edges and applied a 1/2' roundover to the front and sides. The discoloration is a 50/50 mix of carpenters glue and water which I painted on to reduce the edges' inclination to adsorb the paint, which I will spray on tomorrow. The best paint I have found for speaker cabinets is Rustoleum Satin Black. Like the varnish on the cabinets, you apply three coats, wait 72 hours, sand, and apply one final coat.
Same base after initial coats of satin black paint
One pipe with its unfinished speaker mounting baffle and port baffle set in place to check fit. The round speaker mounting baffle will be bolted on to enable me to substitute different size drivers by changing to a different baffle. The port baffle is decorative. Both will be painted satin black for contrast with the natural wood.
The painted port baffles and toilet seats (driver baffles).
Checking the baffles for fit with the driver in place.
The speaker terminals are installed
Driver Single Hex Nut One Quarter
Looking inside the driver baffle at the stuffing, which is lightly inserted in the top section of the pipe, and the eggcrate foam which lines the area of the back directly behind the driver.
Installing the base. It's best to drill out the screw holes in the base to a diameter slightly larger than the screw, so the thread engages only the cabinet bottom and fits loosely in the base itself. Important note: The center of gravity for these enclosures is NOT at the front-back center of the enclosure; it's much closer to the front. It's hard to tell from this picture, but the back of the base is only 1/2' behind the back of the enclosure. For proper balance the front of the base should extend 4' or more out from the front of the enclosure.
The internal wiring with slip-on terminals. I use these initially to facilitate any final adjustments that require me to remove the driver. Then after everything is finalized I will use a direct solder connection to the driver terminals.
The connectors are slipped onto the driver terminals and the driver is installed.
A closer view of the driver mounted on its satin black baffle,and you can also see the subtle grain of the natural birch finish.
A bullet tweeter is recessed into the back to reinforce the very high frequencies and to provide some ambience with reflected sound off the back wall. These are crossed over at about 12khz using a 1.5uF film & foil capacitor and a very small air core inductor (2nd order crossover) and are attenuated to a relatively soft level. Their effect is barely audible but they do add a more realistic effect to the sound of high cymbals, harpsichords, etc.
OUCH! The only thing that didn't turn out as well as I had hoped was the top of the back panel on both speakers. I had to use a handheld circular saw to trim here, and the veneer got chipped. Fortunately it's on the back so you don't see it.
The 'port' really isn't a port at all. It's the mouth of a horn, so this 45 degree reflector really does make sense.
Finally, in the upstairs listening room connected to the Bottlehead Paramours. These speakers are a good match for any 2 watt or greater SET amp.
Fostex FE164 Mass Loaded Tapered Quarter Wave Tube (ML TQWT)
by Martin J. King
Amy Rose in Sonic the He. Amy Rose in Sonic th. Amy Rose in Sonic the Hedgehog 2 (aka Amy in Sonic 2) is a character swap hack Sonic the Hedgehog 2 for the Sega Mega Dr Read more. Pepsi in Sonic 1 Portal Gun in Sonic. A hack based on Sonic the hedgehog 2 made by snkenjoi Aperture Science's Portal Gun finds its way into Sonic 2.The port Read more. There’s plenty to be excited for this year’s showing of ROM hacks and mods for Sonic R, Sonic Heroes, Sonic Adventure DX, Sonic Mania and Sonic Lost World. You can discuss the results of the hacking contest after the jump or via the forum here. Some mods you’ll encounter include ROM hacks of Sonic the Hedgehog 2. Both longtime contenders and newcomers are always accepted so long as you have an account with us at Sonic Retro or Sonic Stuff Research Group. I’m still waiting for the ultimate hack for Sonic Lost World. Jun 30, 2014 ADVENTURE, GENESIS An Ordinary Sonic ROM Hack (beta), Giocare An Ordinary Sonic ROM Hack (beta) Online, Jogar An Ordinary Sonic ROM Hack (beta) Online, Jugar An Ordinary Sonic ROM Hack (beta) Online. Jul rom.
Design and Construction of a Mass Loaded Tapered Quarter Wavelength Tube (ML TQWT) Using the Fostex FE-164 Full Range Driver -- The full technical paper & MathCad model are available for download at www.quarter-wave.com
This tube is Modeled using the author's MathCad Transmission Line Model which is available as a downloadable Mathcad file
Drawing of the As-Built Tube (Fig 1)
Frequency Response -- Actual, Modeled, and a simulation of a same size vented box
Preliminary information generated some interesting discussions on a couple of forums.
The ML TQWT has been updtaed with Baffle Step Compensation.
This tale begins with my Bottlehead S.E.X. amp and a friend commenting that now I've built an amp maybe I should build some speakers. That one quip has led me down the trail of building these speakers and I hope you get some insight on my project and encourage you to build your own.
I spent countless hours cruising web pages in search for a project that had suitable specs. for my Single Ended eXperimenters (S.E.X.) amp, a speaker design that seemed like I could fit them into my living room without damaging the WAF (Wife Acceptance Factor) too much. Then my search led me to the Fostex website .. studying the response curves of their drivers, their excellent assortment of speaker plans etc. Finally, for whatever reason, I chose the Fostex 207E as the driver. In hind sight I suppose the choice was the relatively flat response, the entrance into the beloved 40Hz range, and the electromagnetic shielding that did it for me. After investing in a driver I didn't want to end up with speakers that put my cordless phone and television on the fritz. With the driver chosen I did a search on the internet for existing plans in hopes of finding a fellow DIY'er that has figured everything out for me.
The speakers and the design began with the information found athttp://www.pi.algeriaaudio.com/. Buried in the pages was a Fostex design using the FE207E and the Fostex recommended super tweeter. The design used a pair of book end matched speakers with the driver on the largest side. I was preferential to the look of the Cain-Cain Abby and choose to put the driver on the slanted face instead.
A good friend of mine had me go demo a pair of Von Schweikert speakers which had a rear firing tweeter. I was captivated with the air it gave the room and thought it would be a good idea to try this approach here. After digesting all the web chatter about the bright response from the Fostex drivers .. I figured that the rear firing tweeter would help soften the highs from the whizzer cones too.
I attempted to run the totally overwhelming math cad spreadsheets from Martin King's quarter wave web site and put in my own figures for this design. All in all it was a good lesson in how little I know and how smart others are. Basically the numbers and response curve didn't seem to suggest that I was doing anything too terrible and off to the drawing board I went.
TAKE NOTICE .. something's off with the plans as the original version I thought I was doing had the face of the baffle to the floor .. in the as built version it's cut short of the base. As I recall it was a bit short of making the base so instead of scrapping the otherwise well fit front baffle I trimmed it short. I like the detail but I didn't correct the plans .. or maybe the plans are right on the money for this effect and I measured/cut wrong. Who knows .. they are what they are. Costs and Parts Lists are available in excel if you ask.I have a VERY small work area and even smaller tool storage ability. In all my work area was about 5'x8' so the notion of saw horses, dust free paint shops, and bunches of clamps etc. was out. To this end I ended up having the MDF cut by a pro and I stuck to assembly. I countersunk and tapped before screwing the panels together, gluing the joints when I was happy with the fit up. Even with that precaution there were of course mistakes. Fear not .. BONDO saved the day. One of the rear panels went on a bit off center .. leaving a ridge on one side and a gap on the other. A wood rasp to knock down the big stuff and some bondo and everything was 'true enough' to veneer.
In an attempt to increase the WAF I involved my sweetie in picking the veneer.She chose Lacewood .. I was pleased. In hind sight I would have been better served to learn on something other than Lacewood. The stuff is brittle, expensive, and itchy. But boy does it finish nice.
In the end the project cost a pretty penny by DIY standards .. mostly due to the Lacewood but they turned out well. They sound good .. to me. There's enough choice in tuning them that you should be able to make them sound good to you too. They sounded better when I heard them with a preamp on my system. This hobby is subjective .. there is no perfect. If you like an open, crystal clear sharp high end, with a mid that's emotional but not overbearing then these speakers are for you. If you like to thump your way through your high school and college years they aren't for you. These speakers are for Jazz and in my opinion they do a superb job with it. Regardless, they appear to be very sensitive to twaeks so you should be able to find a happy place for your own preferences. Between stuffing, port tube length, and baffle step correction circuits you should be able to hit the sweet spot. I've ended up naming the speakers LP #9's .. because what could go better with S.E.X. than some love potion??
Thanks to Martin King, Paul Joppa, Terry Cain, and Tim Forman for helping answer my questions. You all are pros.
The following section describes some lessons learned that I hope you find helpful.
Lessons Learned
Screwing .. I do recommend screwing - the box together. Fit the case, drill, countersink, screw, unscrew, glue, screw instead of fussing with a thousand clamps. I glued generous amounts of Elmer's wood glue to both sides of the joint, looking for glue oozing out the sides of the box. After a minute or two to dry you can putty knife off the excess when it's begun to turn plastic and you're as clean as a whistle.
Wood Choice .. I do recommend using MDF for the first run. The stuff is dusty, chips, cracks, and absorbs water. It sure is inexpensive though and if you're happy .. build the next ones out of plywood. It will also convince you to hone your wood working skills so you never have to use it again.
Baffle Step Correction (BSC) .. I ended up not including one .. principally because I only have a 2 W amp and the line level correction just stole too much of the ambiance I was striving for. Some day when I get a more powerful tube amp I'll fiddle around with the speaker level BSC circuit recommended on Martin King's site but for now I'm pleased without it.
Stuffing .. I found the driver to like an empty box. I ended up taking out all the recommend stuffing and leaving only a small piece of polyester (blanket or chair batting) directly behind the driver (about ? long and the width of the box) and just using a staple gun to secure it.
Full Range Driver Single Tqwt Diy Slime Recipe
Room Positioning .. I found the speakers to sound the best to me with a toe in so the intersection was about a yard or so in front of my couch. This seemed to take care of the BSC, brightness, and all the other offenses that the Fostex drivers are accused of having.
Icd 10 Mva Driver Single Vehicle
Speaker Vent Port Tube .. I used the precision port. In hindsight I would put it rear firing so there is some coupling of the bass that is produced with the rear walls. I also fiddled around A LOT with the length of the port tube (both in the math cad software and in the actual box) and found that NO extension sounded best to me. When I added any length to the port tube at all the driver lost nearly all the mid/bass and with it out completely the driver sounded sloppy. So I ended up keeping just the front throat from the precision port as the port tube.
Cutting Driver Holes .. Well, nobody taught me how to cut holes with a router. So I drilled a pilot hole, stuck in the cutting bit and proceeded to drag the router around the circle I had drawn. This worked for about 4 inches until the bit began to smoke. I switched to my dremel with about the same effect. Finally I ended up hacking the hole out with my jig saw. I shared my toils with friends who are still laughing at me not using a circle cutter for my router and cutting the hole a little bit at a time working my way through the material. I'll try that next time.
Full Range Driver Single Tqwt Diy Slime Kit
Cutting Driver Holes Too Wide .. Well .. so much for precision (see section above). I had chosen the hurricane nuts to use on the back side of the panel for putting the mounting machine screws into. I ended up having to bend one side of the hurricane nut up 90 degrees to get the driver into the hole. This worked like a charm and would definitely use the hurricane nut/machine screw combo again.
Internal wire .. I selected some Streetwire 14 gauge stranded OFC tinned wire. I think it sounds good.No, this is not an invitation for speaker wire debate. I recommend using the female disconnects you are supposed to. When you are done with your assembly, finishing, and are putting the speakers together for the last time .. solder the female plug to the speaker .. it makes me feel good that it's on there nice and tight.
Speaker Cup .. Initially I thought that it would be smart to be able to take the super tweeter out of the circuit so I got a speaker cup for bi-wiring. I would not do it again as the L-Pad accomplishes the same thing and it isn't as chincy. Who really uses bi-wiring anyway.
Spikes.. I like the look .. although I suspect there would be more bass if the speaker was sitting on the floor. You choose.
Box Stiffening .. I ended up only using one dowel to stiffen the 'middle' of the sides below the driver. I'm not sure this is worthwhile and may take it out if I do a plywood version some day.
Gauze for Retaining Stuffing .. I used the eyelet screws and tied first-aid gauze to retain the stuffing while I was 'tuning'. I think I like the idea of an acoustically dead material being used here instead of string. It's a bigger surface area for the stuffing to have to leak past and is easy to stretch out of the way if you want to put more/less stuffing into the box. I ended up with no additional stuffing other than a small sheet behind the driver .. again you choose with your earbuds.
Caulk.. Clearly, you must caulk the seams to be sure they are air tight .. problem is that I couldn't see the top inside of the box once assembled, I couldn't steer my caulk gun from the main driver .. I'm open to suggestions here.I ended up cutting a tip off a Ziploc baggie filled with caulk and hand mashing the caulk as high up as I could reach. My guess is there's a glob of caulk stuck to the top of the box stalactite style. It's a trade secret and I'll call it's the Half Assed Touch of Magic (HATM) that must make these speakers sound so good to me.
Box Material .. Like I mentioned before I used MDF. I think next time I'll use plywood. No, I will use plywood because MDF is made by the devil and sucks more than the Sahara in summer. Also, speakers like Audio Note and Cain-Cain aren't made out of MDF .. I figure they may have some clue about this that I don't have.
Veneering .. I enjoyed veneering. I used water cleanup contact cement called Weldwood and got a foam roller to put it on. I used an excess block of wood with the edge sanded a little bit to round it off as the scraping tool and it seemed to work fine .. until I got to the top/bottom edge where I lost track of where the underlying box stopped but the oversized sheet of veneer continued and .. CRUNCH .. I rolled the veneer off the top and folded it over .. leaving a splintered wreck in it's wake. LESSON LEARNED .. full scale practice on cheaper veneer. Next time I will go ahead and press like a son-of .. a-bitch and leave the last 4 inches or so just pressed down with just my fingers then
Invest in a hand held router with a veneer trim bit (thanks to Steve). This tool ROCKS. You simply drag it around the edge and bingo .. perfect edge just waiting for a quick sand. Same goes for finding the holes for the drivers after you are done veneering. Just tap with your fingers until you find the void, cut an X with your utility Knife stick the router bit in the hole, turn it on, drag it to the side and around you go. Presto perfect! To find the holes for the machine screws you may want to make a template of the layout before you veneer so you can use a hand drill to re-drill through the veneer.
If MDF is made by satan. Bondo is God's answer. Use it instead of wood filler .. it's faster, smoother, can be sanded out if you screw it up and re-done. Thanks Steve L. for the bondo suggestion.
Finishing .. I used tung oil but I think Lacewood wants a high gloss .. with less than perfect sanding to start due to the grain and lots of coats with sanding between. Next time .. more gloss, more sanding.
Trolley Driver Single Coin Dispenser
Dowels .. I didn't want to spend another penny on more dowel just for veneering so I improvised a set of “tent cards” fabricated out of photo enlargement sleeves. I think any glossy cardboard could be used instead.This worked perfectly. Once the contact cement has dried for the recommended 40 minutes or so just lay them out and then beginto place the sheet of veneer over the work and then pull them out one at a time.
About Me
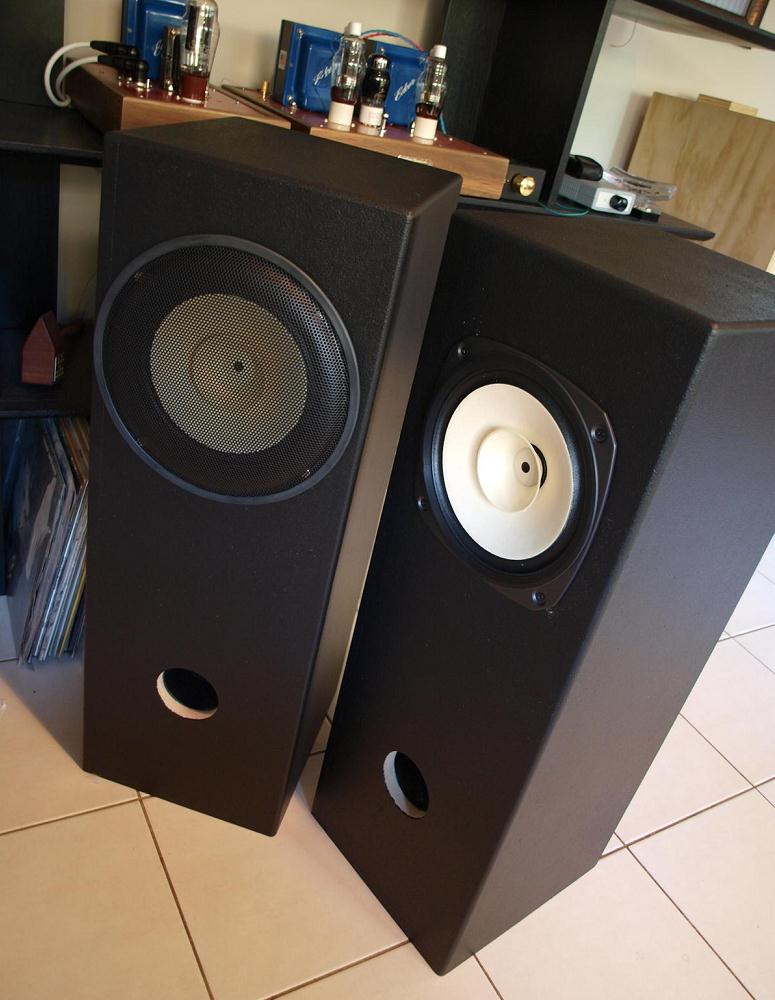
Car And Driver Single Car Seat Cover
- Name:Beltway Bandit
- Location:Washington, DC